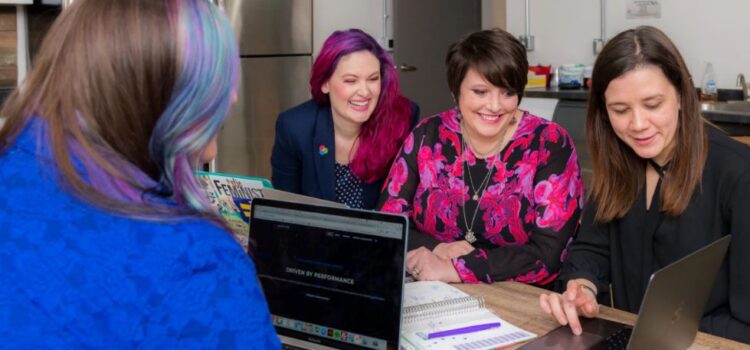
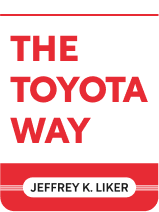
This article is an excerpt from the Shortform book guide to "The Toyota Way" by Jeffrey K. Liker. Shortform has the world's best summaries and analyses of books you should be reading.
Like this article? Sign up for a free trial here .
What is Toyota’s “Respect for People” principle? How does Toyota treat its employees and supply chain partners?
Toyota’s principle, “Respect for People,” is one of the two pillars of the Toyota Way. Jeffrey Liker, in his book The Toyota Way, illustrates how Toyota encourages this principle to build a better company.
Read more on Toyota’s respect for people, most importantly its employees and supply chain partners.
How Toyota Respects Its Employees
According to Liker, Toyota’s respect for people goes a long way. It respects its employees by protecting their jobs, challenging them, and supporting them in their efforts to improve.
Protecting workers’ jobs. Toyota prioritizes job security for its employees, even through significant internal and external challenges. For example, during the Great Recession of 2008-09, while other car manufacturers were letting thousands of people go, Toyota didn’t lay off any members of its regular workforce. Instead, team members worked intensively on kaizen when they weren’t needed on the factory floor. Managers also privately agreed to salary reductions so no team members would be laid off. In the course of normal business, employees whose roles are no longer needed as a result of routine kaizen are redeployed to other assembly lines.
Challenging employees. At Toyota, respecting employees means challenging them. The TPS, with its lack of time buffers and inventory to hide behind, compels employees to think on their feet. Liker says that workers participate in voluntary “quality circles” outside of working hours in which employees work on complex problems together.
Supporting employees. Toyota uses a flipped org chart in which workers on the factory floor are at the top (the highest priority), says Liker. The primary role of a team leader is to support his or her team. Team leaders step in for workers who are sick or on vacation, coach team members in a hands-on way, and routinely watch their team work to prevent problems and improve processes.
Toyota Respecting Employees: Theory vs. Practice
Critics argue that Toyota doesn’t always practice what it preaches when it comes to caring for its employees. Engineer Darius Mehri, who worked as an engineer at a Toyota supplier and interviewed Toyota workers, argues that Toyota endangers its employees with unrealistically fast line speeds. He says up to 50% of its current workers battling work-related health problems. Many have lost fingers or have suffered burn or crush injuries due to attempts to save space in and around their workstations. Mehri also argues that Toyota under-reports injuries (a common practice in Japan).
Protecting jobs. Liker concedes the distinction between the “regular workforce,” whose jobs are protected at all costs, and the “variable workforce,” which consists of temporary employees who can be (and often are) let go quickly. He doesn’t, however, go into detail about temporary employees. Temporary workers constitute over 30% of the assembly line in most Toyota factories in Japan. They make 60% less than the regular employees, don’t receive benefits, and may feel like outcasts or second-class citizens.
Challenging employees. Liker notes that quality circles in Japan are held outside of working hours and are theoretically voluntary. However, all employees are expected to attend. Some critics argue that “challenge” crosses the line into exploitation, potentially endangering the health and even the lives of employees. For example, 30-year-old Kenichi Uchino collapsed and died after working 155 hours of overtime (110 unpaid) one month before his death. Also, a Camry chief engineer died of a heart attack after clocking over 80 hours of overtime the previous month. Multiple workers have also committed suicide due to stress.
Supporting employees. Some argue that Toyota doesn’t support its employees, instead enmeshing them in a net of strict rules that govern what they do both inside and outside work. At work, employees follow “rigid military-style rules” that govern minute details of their behavior inside the factory. Outside of work, employees must report to their managers on details such as their commutes and vacation rest stops.
Toyota’s Respect for Supply Chain Partners
While Toyota is slow to accept new suppliers, first making them “audition” with a series of small orders, once a supplier is in the chain Toyota is loyal and slow to replace them. Toyota shows respect for its supply chain partners by challenging them to engage in intensive kaizen. This helps the supplier increase its own efficiency.
Suppliers are incentivized to engage in kaizen through the “target cost system”: Toyota calculates how much the part should cost in the first year and asks for price reductions each subsequent year (on the basis that the supplier’s kaizen practices should be reducing the cost on their end). Liker comments that Toyota is most suppliers’ favorite customer, despite its exacting standards.
Toyota also supports supply chain partners as needed, for example by making advance payments to suppliers that are struggling or offering financial assistance to dealers during the COVID-19 pandemic.
Unusually, Toyota also respects and helps its competitors, believing that competition makes everyone stronger. For example, Toyota shared hybrid technology with other automakers and opened its hybrid patents in 2019. (Shortform note: A more cynical take on this is that opening the patents was intended to discourage competitors from leaping over hybrid technology and going straight to fully electric vehicles, an area in which Toyota can’t compete well.)
Toyota’s Relationships With Suppliers
Are Toyota’s relationships with its suppliers as healthy as Liker claims? There’s evidence to suggest they might not be. Some suppliers have stated publicly that the target cost system is unrealistic and cruel, especially given inflation and the increasing costs of raw materials. As the manager of one supplier commented in 2010: “Toyota just squeezes us, like it’s trying to wring water from a dry towel.” This approach is especially hard to swallow for suppliers when Toyota continues to post record profits.
Some supply chain workers believe that Toyota’s “just-in-time” system isn’t designed to solve problems but to push them back onto suppliers, which in turn struggle to cope. To reduce costs, some suppliers allegedly hire foreign guest workers, some of whom are victims of human trafficking, and pay them a fraction of the minimum wage, threatening them with deportation if they complain.
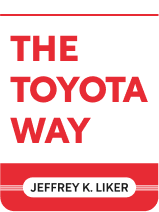
———End of Preview———
Like what you just read? Read the rest of the world's best book summary and analysis of Jeffrey K. Liker's "The Toyota Way" at Shortform .
Here's what you'll find in our full The Toyota Way summary :
- The story of how Toyota became the biggest automaker in the world
- An explanation of Toyota's lean manufacturing process
- Tips on how to apply Toyota's methods to your business