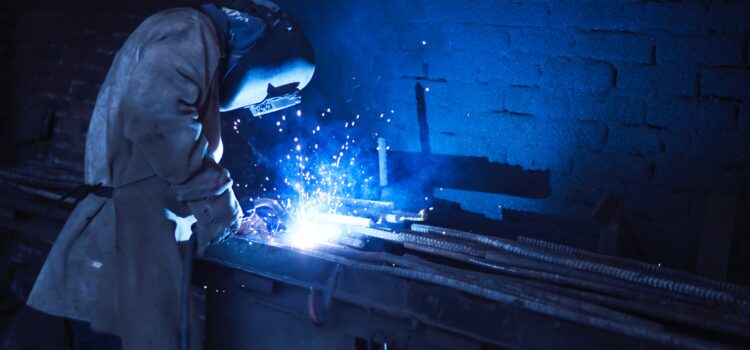
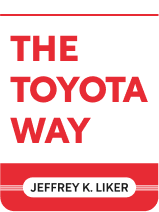
This article is an excerpt from the Shortform book guide to "The Toyota Way" by Jeffrey K. Liker. Shortform has the world's best summaries and analyses of books you should be reading.
Like this article? Sign up for a free trial here .
How does Toyota use lean manufacturing at the factory level? How does it make production more efficient?
In The Toyota Way, engineering professor and lean manufacturing consultant Jeffrey Liker describes the work practices known as lean manufacturing. Liker uses Toyota’s use of lean manufacturing to show how it works.
Below we’ll look at how Toyota’s lean manufacturing is implemented at the modeling stage.
Lean Manufacturing at the Factory Level
The biggest goal of Toyota’s lean manufacturing is to eliminate waste and increase efficiency. This starts with Toyota’s production line.
As Liker explains, Toyota models its production line as a “pull system”: a system in which customer demand for a product “pulls” the product through the assembly line. One example of a typical pull system is a restaurant: A customer’s order for a particular dish sets in motion the processes needed to produce the dish. This contrasts with more traditional “push systems,” in which a manufacturer produces a set number of products and sends them out to be sold, regardless of whether the retailer already has the item in stock.
(Shortform note: Price discounts in stores are often the result of push systems. Many retailers offer discounts to get rid of products quickly when they’ve received a new shipment of products but haven’t finished selling the last round.)
Toyota also uses pull systems to move work in progress from station to station. When workers involved in downstream processes are ready for more parts, they use signals (kanban) to communicate this to upstream workers. Kanban can be as complex as a digital signal or as simple as returning an empty bin to be filled.
The “value stream” is the sequence of actions in the assembly line that add value for the customer. Everything else is seen as waste. Liker explains that Toyota uses value stream mapping to identify which parts of the process add value and which can be minimized or eliminated. To map the value stream, team members draw a box for each workstation in the assembly line. They then go and look at what happens between each process and make notes regarding the transitions between workstations. Are parts transported long distances? Do they wait in queues? Are the workers moving efficiently? They record all of this information in the gaps between the boxes.
One-piece flow is a depiction of the perfect value stream. In one-piece flow, products move through the plant undergoing only processes that add value, with no wasted time or materials. One-piece flow is the opposite of traditional “batch and queue” manufacturing practices, in which large quantities of parts are produced well ahead of time and then sit in queues waiting to be processed. One-piece flow is also called a “just-in-time” system, as each workstation receives the parts just in time to work on them.
The Seven Wastes
Value stream mapping allows you to pinpoint wastes. Liker lists seven types of waste:
- Excess production
- Excess inventory
- Excess movement
- Wasted time
- Inefficient or unnecessary transport
- Inefficient work practices
- Production of defective parts
The goal of lean manufacturing at Toyota is to identify all of the areas of waste and find ways to reduce them.
(Shortform note: In practice, these seven wastes overlap considerably—for example, excess production leads to excess inventory, which is wasteful in part because it delays the detection of defective parts. However, this method of classifying waste is the most common in value stream mapping. You can remember it using the DOWNTIME mnemonic, which includes the eighth type of waste: Failing to make the most of workers’ abilities.)
Calculating Production Line Speed
The three interlocking symptoms of an inefficient value stream are mura (variability), muri (overload), and muda (waste). Liker emphasizes that managing variability is extremely important for Toyota’s lean manufacturing. If the line isn’t operating at a constant speed, at busy times this causes overload, and at idle times it causes waste. Heijunka (leveling), meaning that the assembly line operates at a constant rate and the mix of products is consistent, is the key to minimizing variability.
So the production line should move at a constant pace. But how fast should it move? If the line moves too fast, you risk excess production; if it moves too slowly, you won’t meet customer demand. The right speed for the production line is exactly the rate of customer demand. (Exceeding the rate of customer demand means that parts and finished products sit around in inventory, tying up value and delaying the detection of defects.)
The rate of customer demand as applied to the production line is called takt time. To calculate takt time, work backward from customer demand. For example, let’s say that an assembly line needs to make 600 products per day and the production line operates for 10 hours per day. Dividing 600 by 10, we find that products should be moving through this production line at the rate of 60 products per hour (or one product per minute).
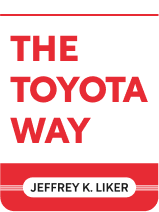
———End of Preview———
Like what you just read? Read the rest of the world's best book summary and analysis of Jeffrey K. Liker's "The Toyota Way" at Shortform .
Here's what you'll find in our full The Toyota Way summary :
- The story of how Toyota became the biggest automaker in the world
- An explanation of Toyota's lean manufacturing process
- Tips on how to apply Toyota's methods to your business