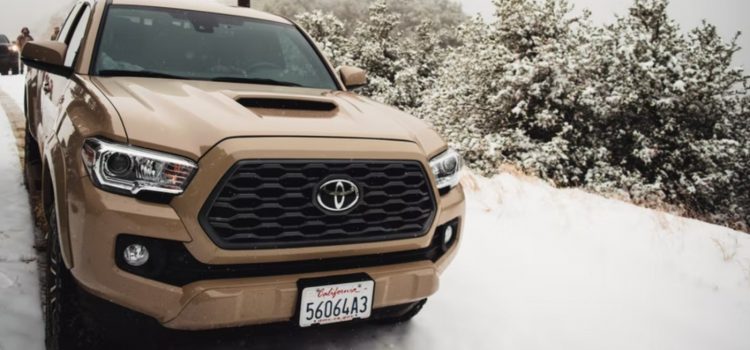
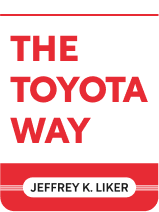
This article is an excerpt from the Shortform book guide to "The Toyota Way" by Jeffrey K. Liker. Shortform has the world's best summaries and analyses of books you should be reading.
Like this article? Sign up for a free trial here .
What is The Toyota Way about? What are the main takeaways from the book?
In his book The Toyota Way, Jeffrey Liker describes how workers at Toyota problem-solve on the spot and ruthlessly eliminate waste. He also explains how the company supports them by offering job security and constant on-the-job challenges.
Keep reading for a brief overview of Liker’s book The Toyota Way.
The Toyota Way Book by Jeffrey Liker
Jeffrey Liker’s book The Toyota Way is a business efficiency classic. Its first edition, published in 2003, rode a wave of intense interest in Toyota’s highly efficient manufacturing processes, which became known as lean manufacturing. Liker’s goal was to clarify Toyota’s approach and rectify the mistakes he saw people making when they emulated the system. The Toyota Way reached a wide audience within and outside manufacturing.
The Toyota Way was the first of Liker’s 15 books on Toyota. In the book’s second edition, published in 2020, Liker reorganized the presentation of some of the principles, updated some of his examples, and explained how Toyota managed recent global crises. This guide is based on the second edition.
Liker discusses the relevant principles of lean manufacturing at three key levels:
- The genba (on the factory floor): This section describes the nuts and bolts of Toyota manufacturing processes, including kaizen (continuous improvement), one-piece flow, and minimizing waste.
- The management level: This section discusses the importance of respecting people, including ensuring job security for employees, challenging workers, and promoting leaders from the inside.
- The level of the whole organization: This section describes the overall vision that guides Toyota and how this vision is integrated throughout the company.
Toyota’s Lean Practices at the Genba
At the heart of Toyota’s approach to efficiency is the concept of kaizen (continuous improvement). Liker describes kaizen as small, incremental improvements in speed and quality that over time add up to large gains. Many assembly line processes are repeated thousands of times a day, so a reduction of even a few seconds for each repetition adds up quickly.
Toyota’s approach to kaizen involves two stages:
- A modeling stage, in which you sketch out the stages of the manufacturing process, identify wastes, and calculate production timeframes. This stage is relatively short.
- A practical implementation stage, in which you test and refine the improvements identified in the modeling stage. This stage is detailed, iterative, and ongoing.
Toyota’s Lean Practices at the Management Level
In Liker’s book The Toyota Way, he says the second level of Toyota’s approach to lean manufacturing is how Toyota manages its people. He covers how Toyota shows respect for its employees, promotes leaders from the inside, prioritizes teamwork and consensus, and extends relationship-building outside the organization to the whole supply chain.
Toyota’s Lean Practices at the Whole-Organization Level
The third level that lean manufacturing operates at is at the whole organization. In The Toyota Way, Liker describes why Toyota is cautious when introducing new technology, how it ensures that goals are consistent throughout the company, and how long-term systems thinking governs high-level decision-making.
Practical Advice for Implementing Lean Systems
To implement lean systems in a business for the first time, Liker recommends the following in his book The Toyota Way:
- Tailor it carefully to your business. Replicating or benchmarking Toyota processes misses the point. As you problem-solve and improve, your version of lean will grow to fit your own business perfectly. It may not look anything like Toyota’s version.
- Start with a cleanup. A big cleanup (ideally using the 5S method) allows you to visually monitor the changes. However, the cleanup is only the beginning.
- Tackle heijunka early. Uneven production is the cause of many wastes. Evening out production is challenging, but doing this first will save time in the long term.
- Start small and be patient. Pilot lean ideas by creating a one-piece flow cell for a small part of the assembly line. Experiment with kaizen inside that cell using Plan-Do-Check-Act cycles.
- Maintain gains through close management. Toyota team leaders monitor their team daily to ensure efficiency gains don’t slide backward.
- Train your employees in problem-solving. If your workers don’t know how to solve problems when jidoka exposes them, production will go down rather than up.
- Make it a priority to coach new leaders. A key role of managers should be to train future managers.
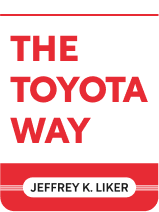
———End of Preview———
Like what you just read? Read the rest of the world's best book summary and analysis of Jeffrey K. Liker's "The Toyota Way" at Shortform .
Here's what you'll find in our full The Toyota Way summary :
- The story of how Toyota became the biggest automaker in the world
- An explanation of Toyota's lean manufacturing process
- Tips on how to apply Toyota's methods to your business