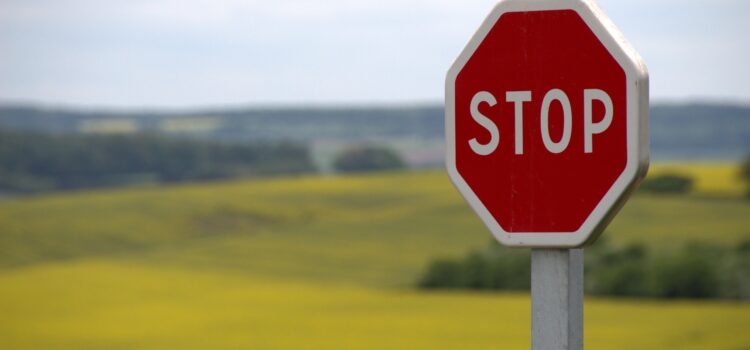
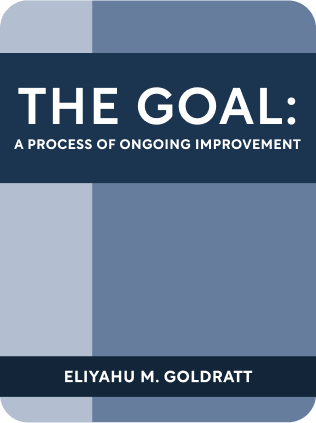
This article is an excerpt from the Shortform book guide to "The Goal: A Process of Ongoing Improvement" by Eliyahu M. Goldratt. Shortform has the world's best summaries and analyses of books you should be reading.
Like this article? Sign up for a free trial here .
What is The Goal Theory of Constraints? How does it work and how can you apply it to improve output?
The Goal Theory of Constraints is the idea that your bottleneck is what determines your output. By focusing on your constraints, you can improve production.
Keep reading for more about The Goal Theory of Constraints and what it means.
What Is The Goal Theory of Constraints?
The critical concept in the book is identifying the bottleneck, or the key constraint that holds back throughput. This is also known as The Goal Theory of Constraints. While this sounds like common sense, it can be hard to objectively identify your own bottlenecks when you’re in the thick of work.
In manufacturing, a balanced plant tries to match the average capacity of every resource exactly with market demand. Any resource beyond the average rate is seen as extraneous, so it is either put to use or eliminated. This is the traditional mode of thinking at the protagonist’s company in The Goal.
However, in The Goal Theory of Constraints, two interconnected concepts make the balanced plant backfire, thus decreasing throughput, increasing inventory, and increasing carrying costs:
- Dependent events – one part of the chain depends on the upstream part.
- The speed of the downstream part is constrained by the upstream part – if the upstream part isn’t delivering, the downstream part can’t do any work.
- Statistical fluctuations – many factors cannot be predicted precisely
- Even at an average steady state rate, there are fluctuations in production. Someone may produce 2 widgets per minute on average, but at times he produces 2.5 and at times he produces 1.
- Larger events – machines may break down; workers many get sick; inclement weather may arrive.
Fluctuations happen regularly at each part in the chain. However, each downstream part can only catch up to the extent that the upstream part permits it to. Negative fluctuations bring down every later step of the chain; positive fluctuations are constrained by the next bottleneck. Over time, this causes a lower than expected average throughput.
The Goal Theory of Constraints With Manufacturing Flow Examples
Relationships between a bottleneck (X) and non-bottleneck (Y) can be summarized in the following 4 diagrams:
Y → X
- The non-bottleneck feeds to the bottleneck
- Y has excess capacity. Letting both X and Y run continuously will build up inventory in front of bottleneck X.
X → Y
- The bottleneck feeds the non-bottleneck.
- Y is starved for inventory to process and marches to the beat of X’s drum. This is totally fine, even if Y is idling at times. No inventory builds up in front of Y.
X → Assembly ← Y
- Parts passing through X and Y flow into a joint step of assembly.
- Working Y out of pace with X produces inventory in front of assembly.
X → Product A | Y → Product B
- Here X and Y are independently operating for separate marketing demands.
- If X cannot produce enough to meet market demand, then the constraint for product A is bottleneck X.
- If Y can produce more than enough to meet market demand, then the constraint for product B is not Y – it is market demand. Y can produce more than the market demands for the sake of “efficiency,” but this will lead to excess product B inventory, increasing costs.
In all these blocks, Y never determines throughput for the system. Throughput instead is determined by bottleneck X, or market demand.
Market Demand and Throughput
Ideally, the flow through the bottleneck should match market demand. Producing more than this will increase inventory of finished product. Too much inventory will hinder flexibility through sunk cost fallacy – you’ll be reluctant to adapt to new market demands, because it would mean writing down your old inventory.
Instead, when you have surplus capacity, try to increase sales to make use of this capacity. Because you’re already paying for the fixed costs, you can lower prices to above material (marginal) cost to simulate more demand. This will decrease your overall cost per product.
Finding the New Constraint
If you do your work right, you’ll find that the constraint is no longer holding up the system, and the constraint has moved somewhere else. This constant process is part of The Goal Theory of Constraints. Here are a few tips on how to deal with this.
Different constraints can require very different optimizations. Don’t assume that what you applied to the first constraint can solve any other constraint.
Don’t overcorrect for the constraint you just fixed. Overcorrection can be counterproductive. If you obsess about preventing the bottleneck from idling and exceed market demand, you’ll produce surplus inventory.
Five Focusing Steps for Improvement
In The Goal Theory of Constraints, Goldratt describes the 5-step process for continuous improvement:
- IDENTIFY the system’s constraint.
- OPTIMIZE the system’s constraint. Squeeze more capacity out of the constraint.
- SUBORDINATE all the non-constraints to the above decisions.
- ELEVATE the system’s constraint. Add more capacity to the constraint.
- If in the previous steps the constraint no longer remains the constraint, go back to step 1 for the new constraint.
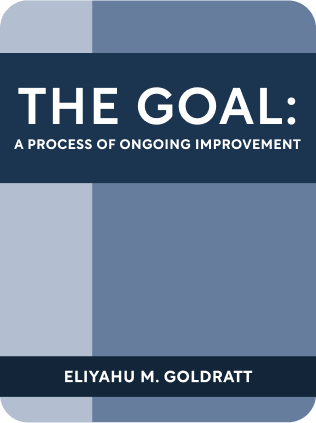
———End of Preview———
Like what you just read? Read the rest of the world's best book summary and analysis of Eliyahu M. Goldratt's "The Goal: A Process of Ongoing Improvement" at Shortform .
Here's what you'll find in our full The Goal: A Process of Ongoing Improvement summary :
- How to increase your personal output
- How to increase your team's output
- Why obsessing over cost efficiency isn't going to help you with production