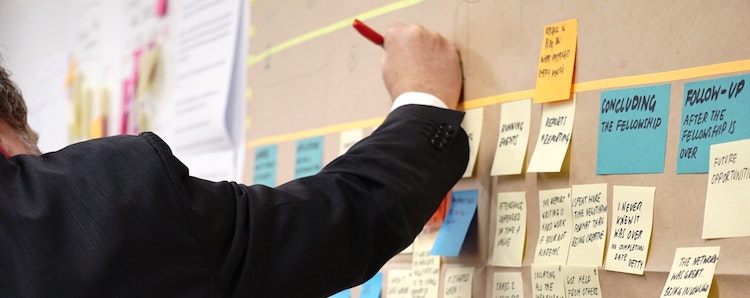
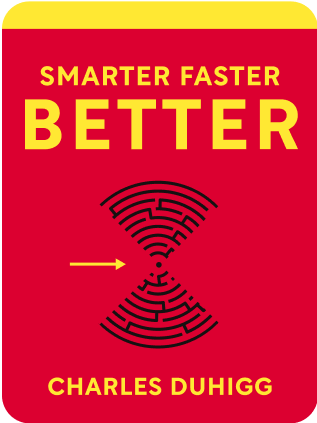
This article is an excerpt from the Shortform book guide to "Smarter Faster Better" by Charles Duhigg. Shortform has the world's best summaries and analyses of books you should be reading.
Like this article? Sign up for a free trial here .
How does a lean management system maximize efficiency and productivity? What are its limitations?
In Smarter Faster Better, Charles Duhigg explains how a lean management system contributes to productivity. He highlights one aspect of the lean method that he believes rises above the rest. Duhigg also provides a real-world example of the system and lays out its limitations.
Read more to learn how a lean management system can boost productivity.
What Is a Lean Management System?
Also known as the Toyota Production System due to its origins in the company of the same name, a lean management system (or lean manufacturing) is a system designed to maximize efficiency and productivity. It’s enabled Toyota to cut costs while keeping quality high.
Lean manufacturing is a complex philosophy that’s made up of many important elements. However, Duhigg chooses to highlight one aspect of this ideology that he believes is crucial to productivity: giving the worker closest to a problem the decision-making authority to solve it.
This method of decision making is based on the idea that the person closest to a given system or machine is likely to have the strongest knowledge of it. Therefore, if something goes wrong, they’re in the best position to fix it. The system utilizes every worker’s expertise, from executives to janitors.
Implementing this element of a lean management system has various benefits. For one, it makes day-to-day work more efficient. Workers don’t have to wait around for permission from on high to make their decision. They can get started on fixing issues straight away.
Crucially, this system also has the benefit of giving every employee a little bit of decision-making power. Every worker is allocated some authority, and thus a little bit of control. As we learned in Chapter 1, feeling in control fuels our motivation—and if we’re motivated, we’re likely to be more productive.
The lean method has proved to be so successful that it’s been adapted for other industries. For example, the Agile management ideology that’s often used in the software industry is largely based on this system. However, there are some caveats to lean manufacturing’s success.
What Are the Limitations of the Lean Method?
Implementing lean manufacturing isn’t as simple as giving workers the power to make decisions and expecting things to change overnight. Just because workers have this power doesn’t automatically mean they’ll feel comfortable using it. They might be afraid of negative consequences if things go wrong—if they make the wrong decision, or if their “right” decision has unexpected drawbacks.
For a lean management system to truly work, workers need to feel respected and trusted. They need to feel that their employer will have their back regardless of the effects of their decisions. They should feel that managers are committed to helping them improve and learn from their mistakes, rather than just punishing them. They should also be assured that when they make good decisions, they will be recognized and respected for it, and not just ignored. One way to generate this atmosphere of trust and respect is to create a commitment culture.
Example: Transforming the Fremont Car Manufacturing Plant
In the mid-1980s, General Motors and Toyota partnered up to reopen a car plant in Fremont, California. They called their new venture the New United Motor Manufacturing, Inc., or NUMMI.
The Fremont plant had closed two years earlier due to a myriad of issues:
- Workers had taken no care in the work they did and had sometimes actively sabotaged the cars.
- Workers had drunk alcohol, taken drugs, and had sex while on the job.
- Productivity was low due to a prevailing attitude of “the production line never stops.” Even if workers spotted an issue with a car part, they couldn’t fix the problem until the car had reached the end of the production line. This often meant that the car had to be deconstructed to reach the faulty part and then reconstructed again—a time-consuming process.
Toyota planned to revolutionize the plant by introducing a lean management system. However, due to a union agreement, 80% of the reopened plant’s laid-off workers had to be re-employed. This meant Toyota had to introduce lean manufacturing to the misbehaving workers who’d become used to a completely different system.
Introducing the Lean Method
As a first step, the Fremont plant’s employees were sent to a Toyota plant in Japan for two weeks to witness a lean management system in action. One such employee was Rick Madrid, who’d worked at the Fremont plant back in its pre-NUMMI days.
Madrid was shocked by what he saw in the Japanese plant. He witnessed the workers closest to a problem being empowered to make decisions on how to fix it. All workers had the power to stop the production line and fix issues as they spotted them. They simply had to pull on a hanging cord—called an “andon cord”—and the line would eventually grind to a halt.
Madrid also witnessed respectful collaboration between workers and their managers. If a worker was fixing an issue, they could give orders to their manager and the manager would help them. Such collaboration never would have happened at Fremont in its pre-NUMMI days, when managers had shown no respect to their workers.
Finally, Madrid noticed that workers at the plant were encouraged to suggest improvements to boost the productivity of the production line. For example, one worker suggested a new tool for installing struts. The next morning, all workers were given a version of the tool. In the past, managers at the Fremont plant had ignored their workers’ suggestions.
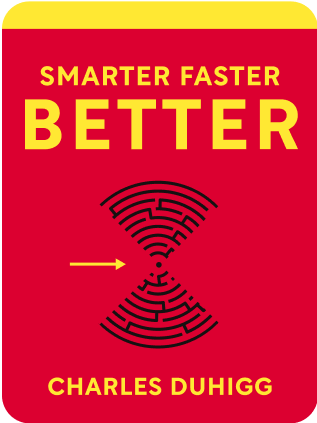
———End of Preview———
Like what you just read? Read the rest of the world's best book summary and analysis of Charles Duhigg's "Smarter Faster Better" at Shortform .
Here's what you'll find in our full Smarter Faster Better summary :
- Why becoming more productive isn’t about working longer hours or constantly pushing yourself to do more
- The 8 principles for improving productivity
- How to create a work culture in which each employee is truly valued