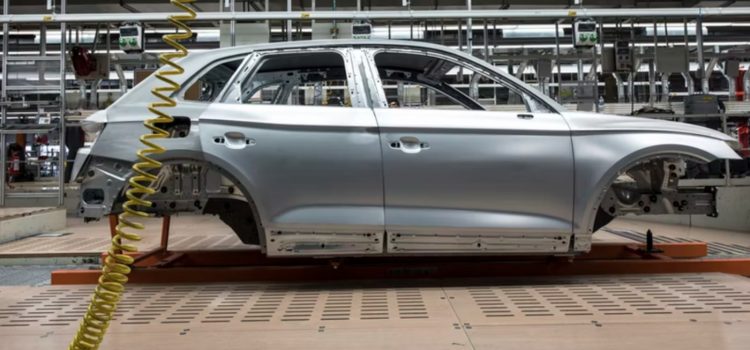
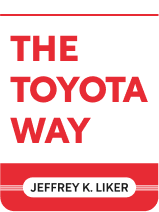
This article is an excerpt from the Shortform book guide to "The Toyota Way" by Jeffrey K. Liker. Shortform has the world's best summaries and analyses of books you should be reading.
Like this article? Sign up for a free trial here .
What does “kaizen” mean? Why is it one of the pillars of the Toyota Way?
In The Toyota Way, kaizen is described as continuous improvement. Author Jeffrey Liker says kaizen improves Toyota’s operations at both the modeling stage and the implementation stage.
Here’s more on the concept of kaizen in The Toyota Way.
Toyota’s Approach to Kaizen
At the heart of Toyota’s approach to efficiency is the concept of kaizen. The Toyota Way describes kaizen as small, incremental improvements in speed and quality that over time add up to large gains. Many assembly line processes are repeated thousands of times a day, so a reduction of even a few seconds for each repetition adds up quickly.
Toyota’s approach to kaizen involves two stages:
- A modeling stage, in which you sketch out the stages of the manufacturing process, identify wastes, and calculate production timeframes. This stage is relatively short.
- A practical implementation stage, in which you test and refine the improvements identified in the modeling stage. This stage is detailed, iterative, and ongoing.
We’ll introduce the theoretical tools that Toyota uses to model assembly line processes. We’ll then talk about how Toyota workers implement these processes and experiment with them on the shop floor.
The Modeling Stage
As Liker explains in The Toyota Way, kaizen is instrumental in the production line. Toyota models its production line as a “pull system”: a system in which customer demand for a product “pulls” the product through the assembly line. One example of a typical pull system is a restaurant: A customer order for a particular dish sets in motion the processes needed to produce the dish. This contrasts with more traditional “push systems,” in which a manufacturer produces a set number of products and sends them out to be sold, regardless of whether the retailer already has the item in stock.
Toyota also uses pull systems to move work in progress from station to station. When workers involved in downstream processes are ready for more parts, they use signals (kanban) to communicate this to upstream workers. Kanban can be as complex as a digital signal or as simple as returning an empty bin to be filled.
The “value stream” is the sequence of actions in the assembly line that add value for the customer. Everything else is seen as waste. Liker explains that Toyota uses value stream mapping to identify which parts of the process add value and which can be minimized or eliminated. To map the value stream, team members draw a box for each workstation in the assembly line. They then go and look at what happens between each process and make notes regarding the transitions between workstations. Are parts transported long distances? Do they wait in queues? Are the workers moving efficiently? They record all of this information in the gaps between the boxes.
One-piece flow is a depiction of the perfect value stream. In one-piece flow, products move through the plant undergoing only processes that add value, with no wasted time or materials. One-piece flow is the opposite of traditional “batch and queue” manufacturing practices, in which large quantities of parts are produced well ahead of time and then sit in queues waiting to be processed. One-piece flow is also called a “just-in-time” system, as each workstation receives the parts just in time to work on them.
The Seven Wastes
Value stream mapping allows you to pinpoint wastes. Liker lists seven types of waste:
- Excess production
- Excess inventory
- Excess movement
- Wasted time
- Inefficient or unnecessary transport
- Inefficient work practices
- Production of defective parts
When you map the value stream, the goal is to identify all of the areas of waste and find ways to reduce them.
The Implementation Stage
The second part of Toyota’s approach to kaizen is at the implementation stage. The common way to start kaizen is the 5S cleanup process:
- Seiri (sort): Get rid of unnecessary items.
- Seiton (systematize): Devise a logical system for storing and displaying the necessary items.
- Seiso (shine): Make sure everything stays in its place. Fix broken items.
- Seiketsu (standardize): Record rules and instructions and share them with everyone who uses the space.
- Shitsuke (sustain): Ensure that no parts of the system are allowed to deteriorate.
Liker comments that some lean consultants go into a business, do this cleanup, and declare kaizen complete—but this is just the starting point.
Jidoka (Intelligent Error Detection)
In Toyota’s approach to kaizen, it’s crucial to expose defects early. Liker explains that in traditional manufacturing processes, large piles of inventory can hide defects that aren’t discovered until much later, making it hard to trace the cause of the problem. Toyota roots out defects by deliberately keeping inventory levels low and through jidoka (intelligent error detection).
Sakichi Toyoda’s loom—designed to stop automatically when it detected a single broken thread—is the prototypical example of jidoka. When the loom stopped, this was a signal that something was wrong and a call to fix the problem.
Applied to the assembly line, Liker calls this concept “in-station quality,” meaning that at each workstation, both people and machines inspect each newly received part and stop the line immediately if they detect a problem. Standard Toyota practices such as maintaining minimal inventory levels and a clear line of sight across the shop floor also help workers and supervisors to spot problems early. The signaling mechanisms that alert others that something is wrong (pushing a button, pulling a cord, automatic alarms) are called andon. When an andon is activated, other team members come running to help solve the problem.
Liker points out that in terms of efficiency, this practice seems counterintuitive: How can an assembly line be efficient if it stops every time someone spots a defect? He argues that in the short term, stopping the assembly isn’t efficient. However, stopping the production line adds urgency to the problem-solving process, so problems are solved much faster than they would be if the line hadn’t been stopped. And in the long term, quickly detecting and solving errors dramatically improves the efficiency of the whole line.
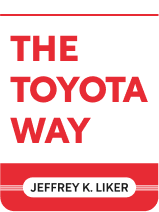
———End of Preview———
Like what you just read? Read the rest of the world's best book summary and analysis of Jeffrey K. Liker's "The Toyota Way" at Shortform .
Here's what you'll find in our full The Toyota Way summary :
- The story of how Toyota became the biggest automaker in the world
- An explanation of Toyota's lean manufacturing process
- Tips on how to apply Toyota's methods to your business