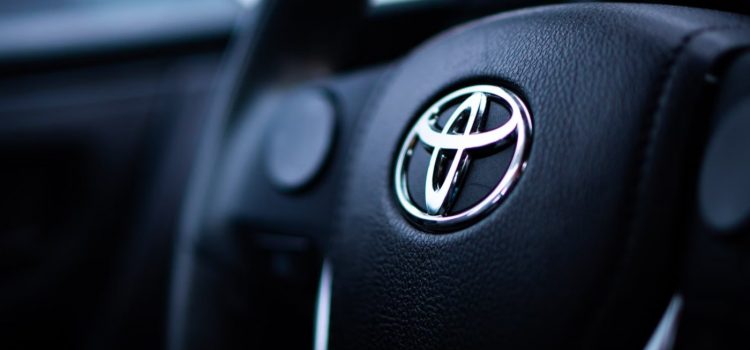
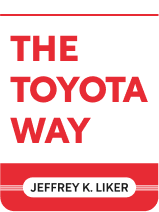
This article is an excerpt from the Shortform book guide to "The Toyota Way" by Jeffrey K. Liker. Shortform has the world's best summaries and analyses of books you should be reading.
Like this article? Sign up for a free trial here .
Why is Toyota successful? What is Toyota’s approach to business?
Toyota is one of the biggest and most successful car manufacturers in the world. It’s successful because it values all of its employees, is cautious of new technology, and has a long-term plan.
Learn more about why Toyota is successful, according to Jeffrey Liker in The Toyota Way.
1. Toyota Takes a Cautious Approach to Technology
Why is Toyota successful? One reason is that Toyota sees large investments in technology, for example, specialized robots, as risky. The company learned this lesson in 1991 when a new, highly automated Lexus plant had to be shut down due to an economic downturn. This mistake taught Toyota that technology should support people, not replace them, and the company is now much more selective in using new technology. Simpler tasks that need limited space can be delegated to robots. However, for more complicated tasks, people are a more flexible resource.
2. Toyota Aligns Goals and Learns as a Whole Organization
At Toyota, managers ensure that people’s goals are aligned through hoshin kanri (policy deployment). This means that managers and workers are in continuous dialogue about the shifting priorities of the organization. Unlike most other Toyota processes, hoshin kanri operates in a top-down manner. The author explains that high-level management determines strategic priorities on a yearly basis at the start of the fourth quarter, communicates them to the whole organization, and then trusts managers to cascade them down into on-the-ground realities.
(Shortform note: Toyota’s combination of bottom-up consensus decision-making and top-down hierarchical decision-making is one of its strengths. Some Japanese companies rely too heavily on consensus decision-making, which makes them slow to adapt to changing circumstances. Some experts even argue that it was Japanese electronics company Sharp’s top-down decision-making style that caused the company to fail.)
At Toyota, kaizen applies everywhere, not just at the genba. All Toyota workers are charged with experimenting and continuously improving systems using Plan-Do-Check-Act cycles, meaning that learning occurs at the level of the whole company.
Liker argues that hansei (“critical reflection”), a Japanese cultural practice, supports the drive toward constant improvement. When Japanese children behave badly, they’re told to “do hansei,” which means they should feel very sorry about what they did and think hard about how they can improve. (Liker notes that Japanese Toyota managers had considerable difficulty in teaching hansei to US managers.) Toyota holds hansei meetings after trying out new ways of doing things, even if the innovation was a success, to identify ways in which it could have been done even better.
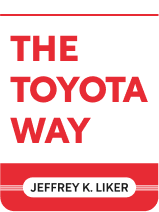
———End of Preview———
Like what you just read? Read the rest of the world's best book summary and analysis of Jeffrey K. Liker's "The Toyota Way" at Shortform .
Here's what you'll find in our full The Toyota Way summary :
- The story of how Toyota became the biggest automaker in the world
- An explanation of Toyota's lean manufacturing process
- Tips on how to apply Toyota's methods to your business