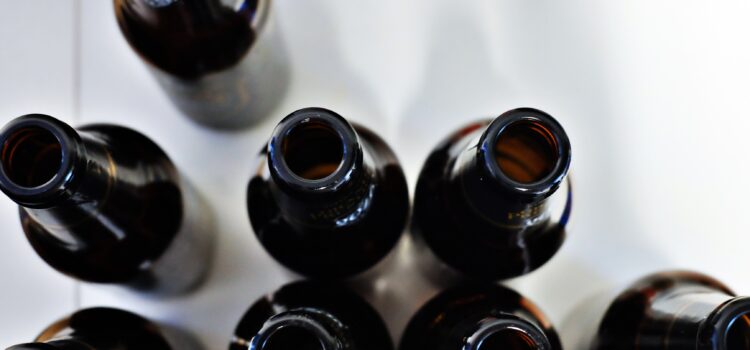
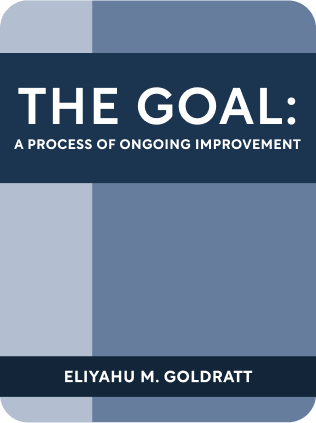
This article is an excerpt from the Shortform book guide to "The Goal: A Process of Ongoing Improvement" by Eliyahu M. Goldratt. Shortform has the world's best summaries and analyses of books you should be reading.
Like this article? Sign up for a free trial here .
What is bottleneck management? What are the different strategies for handling bottlenecks?
Bottleneck management is the process of improving the parts of your process that hold everything else up. Either you fix the bottleneck in the process or you work around it.
Keep reading for tips for bottleneck management from The Goal.
Bottleneck Management With Fixes
We can divide bottleneck management that targets the backlog into a few themes.
Improve the Bottleneck in the Process
- Skip unnecessary steps or decreasing setup/switching costs.
- Add on supplements to increase bottleneck capacity, even if they’re less efficient
- Guarantee round-the-clock production at the bottleneck.
- Example: Eliminate lunch breaks and downtime.
- Permanently staff people at bottlenecks to decrease idle time.
- Eg have people waiting by dishwasher to prepare loads and unload immediately.
- Remember that the cost of a lost hour at this bottleneck is very expensive, and possibly well worth people idling on standby.
Improve What the Bottleneck is Working On
- Focus the bottleneck only on parts that are needed today, not for safety’s sake tomorrow.
- Order the work in terms of first in, first out – clear the backlog first to guarantee important work is being done.
- Allow parts to skip the bottleneck step if it’s not necessary.
- Collect accurate statistics on bottleneck operations to make better decisions.
Optimize the System for the Bottleneck
- Redistribute capacity from non-bottlenecks to the bottleneck (e.g. more workers).
- Make sure there is extra inventory ahead of the bottleneck so it can always be running at full capacity.
- Take some of the load on the bottleneck and redistribute to non-bottlenecks, if the same function can be performed.
- Do quality control upstream of the bottleneck to prevent time processing substandard parts.
- Tag parts that will go to the bottleneck as higher priority, so they get processed first and you guarantee inventory in front of the bottleneck. The bottleneck gets an express lane.
- Announce the importance of bottleneck to the entire team, so they understand the priority of processing for the bottleneck.
- Check upstream steps to see if adjustments can be made that decrease load on bottleneck.
- In The Goal, the team discovers that running an upstream milling step more efficiently leads to requiring heat treatment. If this is slowed down, then the parts can skip heat treatment. In this case, lowering efficiency at one step actually increases throughput.
- Outsource the bottleneck outside the organization.
(Shortform suggestion: take some time to consider how to apply these to your own life. For example, say you’re a manager who wants to improve your throughput. Consider the above fixes directly applied to a manager, whose time can often be the bottleneck of an organization’s throughput:
- Increase your time on tasks that you are uniquely good at (ideally, these are higher leverage tasks). Train others to take over your lower level responsibilities.
- Allow workers to bypass you for permission for smaller decisions. Don’t require everything to pass by your desk.
- Prevent idle time by enforcing meetings starting on time with everyone present.
- Track your backlog so that more important items are worked on first, then process in first-in first-out order.)
Bottleneck Management by Structuring Around the Bottleneck
Once you identify the bottleneck and improve its capacity, you may find other problems arising that decrease throughput. In the narrative, the team goes through multiple iterations of solving problems with bottleneck management, yielding the below principles.
Keep Non-Bottlenecks Synchronized with the Bottleneck
In the story, the team identifies a robot as the bottleneck. They devise a system whereby all parts destined for the bottleneck are always worked on at highest priority at non-bottleneck steps. This increases throughput temporarily, until they discover that at final assembly, suddenly there are shortages in non-bottleneck parts while there is massive inventory upstream of the bottleneck. How could this be?
They discover that they were running non-bottlenecks at full-speed and cranking out bottleneck parts far in excess of what the bottleneck could process. In turn, the non-bottlenecks had insufficient capacity to produce their non-bottleneck parts.
To avoid this, bottleneck management says that you must synchronize the non-bottlenecks with the bottleneck, to prevent massive deviations. Goldratt proposed the Drum-Buffer-Rope method.
The Four Components of Processing Time for Bottleneck Management
Each piece of material spends time from when it enters a plant to when it leaves:
- Setup time: the resource prepares itself to work on the part
- Queue time: the part waits for a resource while the resource is busy
- Process time: the part is being modified to become more valuable
- Wait time: the part waits for another part to be assembled together
All types of time add cost to the system and lower throughput.
For parts going through bottlenecks, queue time is dominant. For non-bottlenecks, wait time is dominant.
Cutting Batch Sizes
Traditionally, larger batch sizes are seen as more efficient per part. However, this decreases agility and increases inventory.
Imagine cutting batch sizes in half, and the benefits that result:
- You’ll halve the work-in-process inventory, which will ease cashflow.
- You reduce queue and wait times for parts.
- You reduce lead time from order to delivery.
- One drawback: this will require more frequent deliveries from suppliers.
But wait – won’t cutting batch sizes increase setup time at non-bottlenecks? This isn’t really an issue. Remember, an hour saved at a non-bottleneck is a mirage. Reducing an hour at a non-bottleneck doesn’t increase throughput, because the bottleneck determines throughput.
(For what it’s worth, cutting batch sizes also decreases idle time, since non-bottlenecks are kept busier rather than waiting for the big batch upstream.)
Appearance of a New Bottleneck in the Process
When you increase capacity at the bottleneck in a process, you may start seeing shortages in non-bottleneck parts that hold up other parts of the chain.
While by reflex you might think this is a new genuine bottleneck, be wary – often production has so much extra capacity that it takes a huge increase in throughput before this really happens.
For example, in the plot of the The Goal, a non-bottleneck is producing two parts – part Y that goes through a non-bottleneck chain, and part X that goes through a bottleneck. If you focus the non-bottleneck entirely on part X, then you create a scarcity of the non-bottleneck parts Y – which creates an artificial bottleneck.
Instead, ideally you synchronize all parts that run through all chains so that the right number of parts reach the last step at the same time to meet market demand (with some buffer).
Similarly, taking on more orders may reduce spare capacity on non-bottlenecks, depleting inventory in front of the bottleneck and starving it of work.
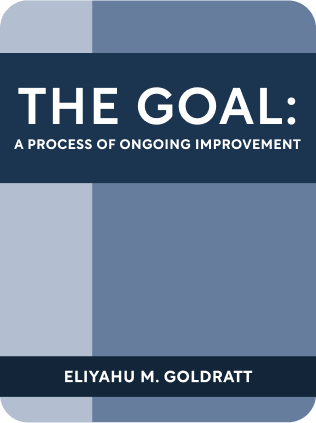
———End of Preview———
Like what you just read? Read the rest of the world's best book summary and analysis of Eliyahu M. Goldratt's "The Goal: A Process of Ongoing Improvement" at Shortform .
Here's what you'll find in our full The Goal: A Process of Ongoing Improvement summary :
- How to increase your personal output
- How to increase your team's output
- Why obsessing over cost efficiency isn't going to help you with production